ABOUT US
WHO WE ARE
We are a company with over 125 years of experience in steel processing and cold bending of sections.
We have 16 branches across Europe and employ over 450 people.
We invite you to familiarize yourself with our offer of sections for the production of container frames, in addition, our production also includes cold-formed sections, roof purlins (Z-profiles, Z-sections) and wall transoms (C-profiles, U-sections), flashings, steel façades, aluminium façades, bases for continuous skylights, photovoltaic constructions.
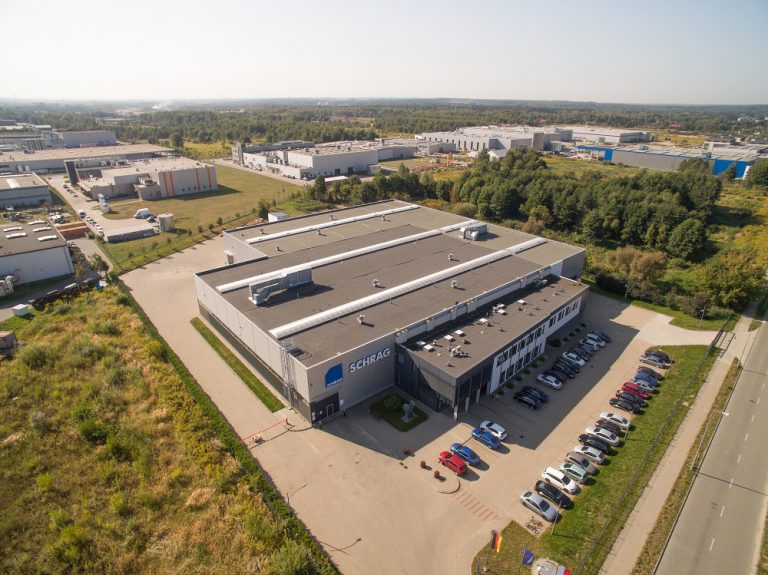
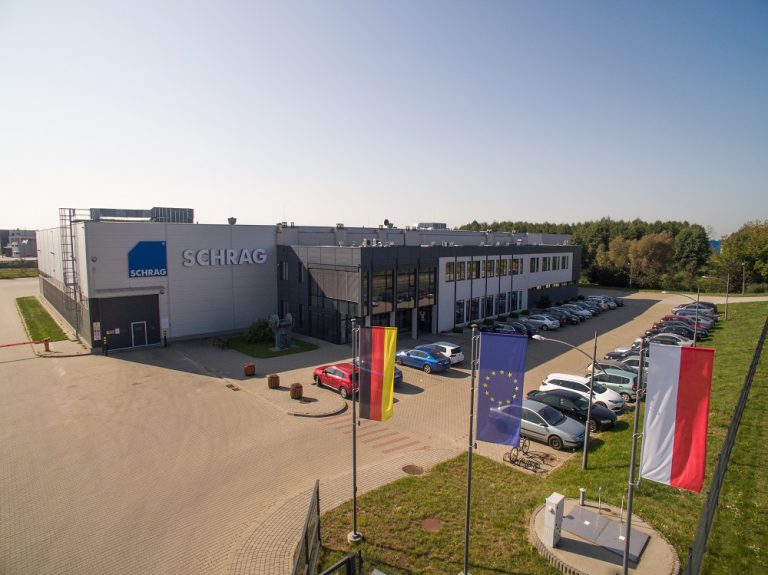
MODERN PRODUCTION PROCESS
We have been manufacturing cold-formed sections since the 1960s. Currently, they constitute the main scope of our production. We have a fully computerized machine park that allows us to obtain very high dimensional accuracy and repeatability of sections.
WHY US
WHO WE ARE
Our experience
Our experience
Our experience in steel processing dates back to 1892
Know-How
Our know-how
It has been acquired and passed down for several generations
Technical support
Our advisors
They are at your disposal 5 days a week
CONTAINER PROFILES
TYPES
An alternative solution offered by Schrag Polska are steel container profiles manufactured in the form of cold-formed sections. The starting material is a flat steel sheet with appropriate strength parameters, thickness and grade.
The advantages of cold-formed container profiles:
- manufactured individually, tailored to each order
- great freedom of shape of the cross-section
- variable sheet metal thickness and grade
- element lengths tailored individually to each project
- low weight of profiles
- relatively low price
Depending on the thickness of the sheets and the shape and dimensions of the cross-section, we manufacture sections using two technologies:
- edge bending
- continuous profiling
The edge bending technology is more versatile. It allows for more complex cross-sectional shapes and covers a wider range of sheet thicknesses. However, it is more time-consuming than continuous profiling technology and requires more effort. Compared to continuous profiling, it is much more versatile, more shapes can be made. Starting from roof purlins (Z-profiles, Z-sections), wall transoms (C-profiles, U-sections) through flashings, steel façades, aluminium façades, steel container profiles, substructures for photovoltaic systems and bases for continuous skylights.
Continuous profiling technology is less time consuming. Thanks to it, sections can be produced in a much shorter time compared to edge bending. The advantage of this method is the possibility to obtain longer lengths of elements, but it is associated with large limitations of shapes and dimensions of the cross-section. This technology is most often used to manufacture roof purlins (Z-profiles, Z-sections), wall transoms (C-profiles, C-sections), 2x bent C-profiles (also as container profiles).
In addition, we drill holes, make undercuts and bevels in the sections we manufacture. We manufacture sections to specific orders based on the documentation provided by the customer. The elements are individually adapted to each project.
Sheet metal grades and thicknesses
The most commonly used steel grade is: S235 and S355, moreover, container profiles can also be made of DX51D, S350GD or S390GD galvanized steel sheets.
The thickness of the sheets used ranges from 1.0 to 4.0 mm.
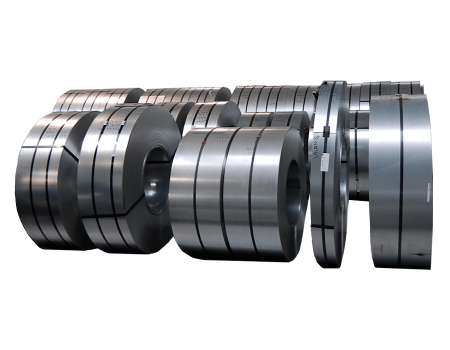
BUILD YOUR SUCCESS WITH US
Schrag Polska - cold-formed sections
Upper beam
One of the characteristic and most frequently produced cold-formed container profiles is the upper beam (circumferential gutter). It is the most complex element of the entire frame due to its cross-sectional shape. It serves as both a load-bearing element of the container frame and an additional perimeter gutter that collects and drains water from the roof. This solution greatly facilitates and speeds up the construction of the container. Making the perimeter gutter as a single element welded only in the corners ensures its tightness and functionality. The use of cold-formed open sections as container profiles also has a positive effect on the possibility to protect steel against corrosion. After welding and processing, the container frame can be easily protected, e.g. by cleaning all easily accessible surfaces and then applying protective paint coats. The perimeter gutter is most often made of “black” sheet metal. If you want to obtain additional anti-corrosion protection, it can be made of galvanized steel sheets.
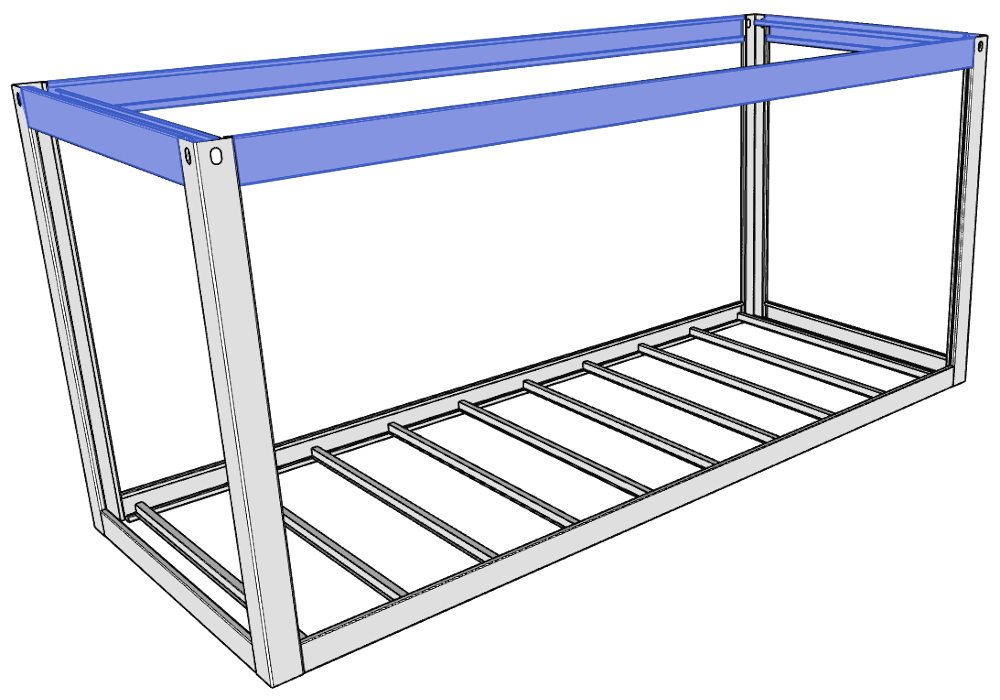
Lower beam
Another cold-formed container profile is the lower perimeter beam. It mainly performs the load-bearing function for the entire container. At the customer’s request, we can also make undercuts and bevels that facilitate the assembly of subsequent elements, e.g. transverse stiffening ribs or electrical, or water and sewage systems. It does not have such complicated shapes as the upper gutter, but due to the open shape of the cross-section, it is also easy to process and protect with protective paint coats. It is most often made of “black” sheet metal, but it can also be made of galvanized steel sheets for additional anti-corrosion protection.
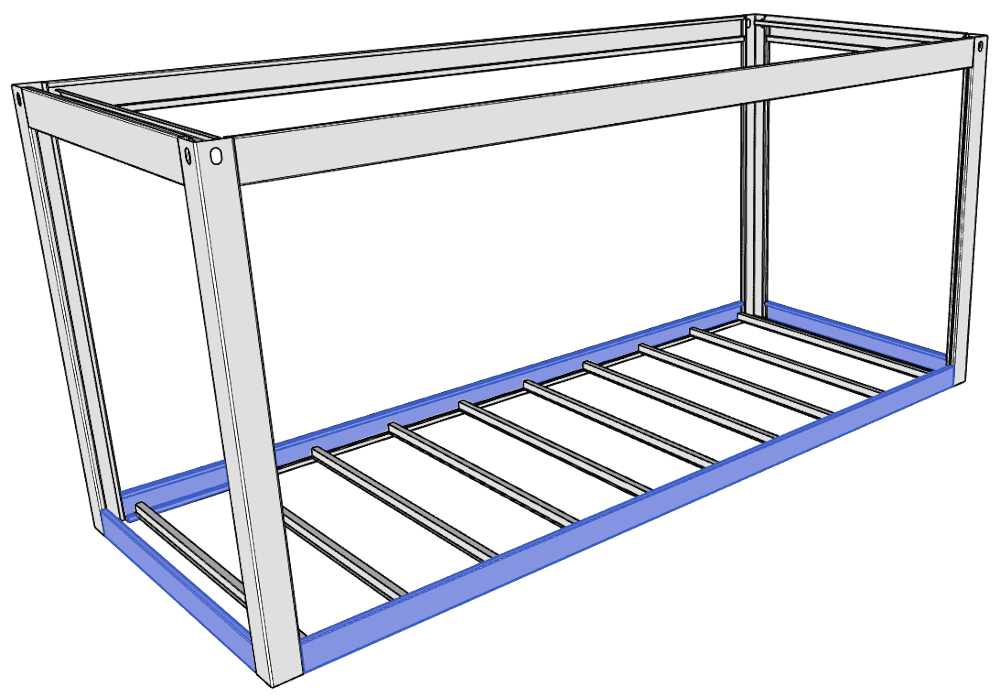
OUR ACHIEVEMENTS
100%
SATISFIED CUSTOMERS
25,000 TONS
OF MANUFACTURED PROFILES
22 YEARS
OF EXPERIENCE
Uprights
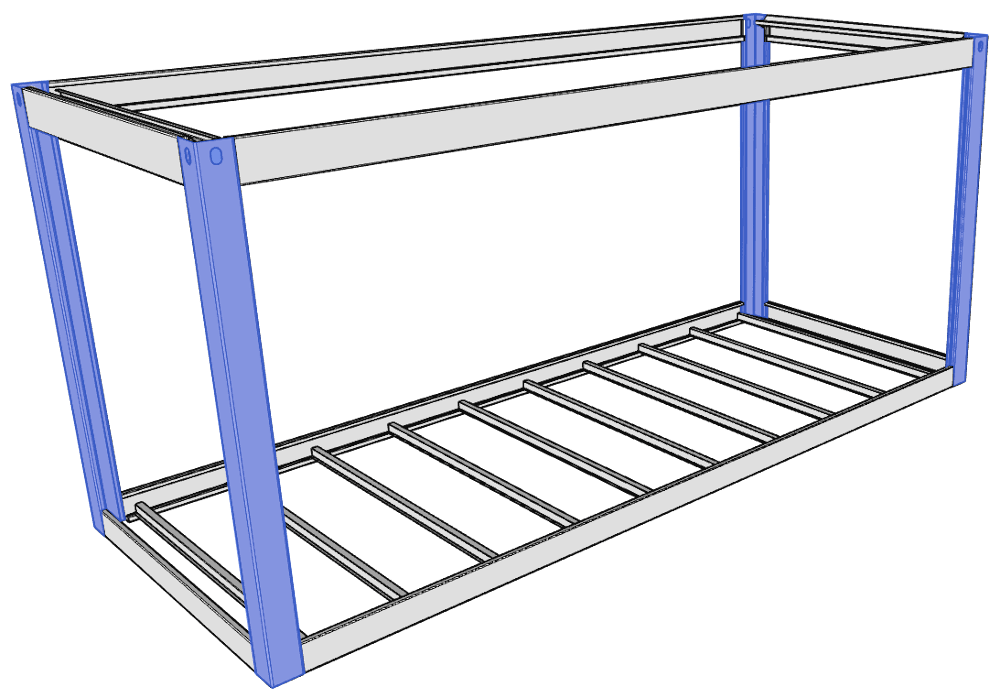
Reinforcing crossbars
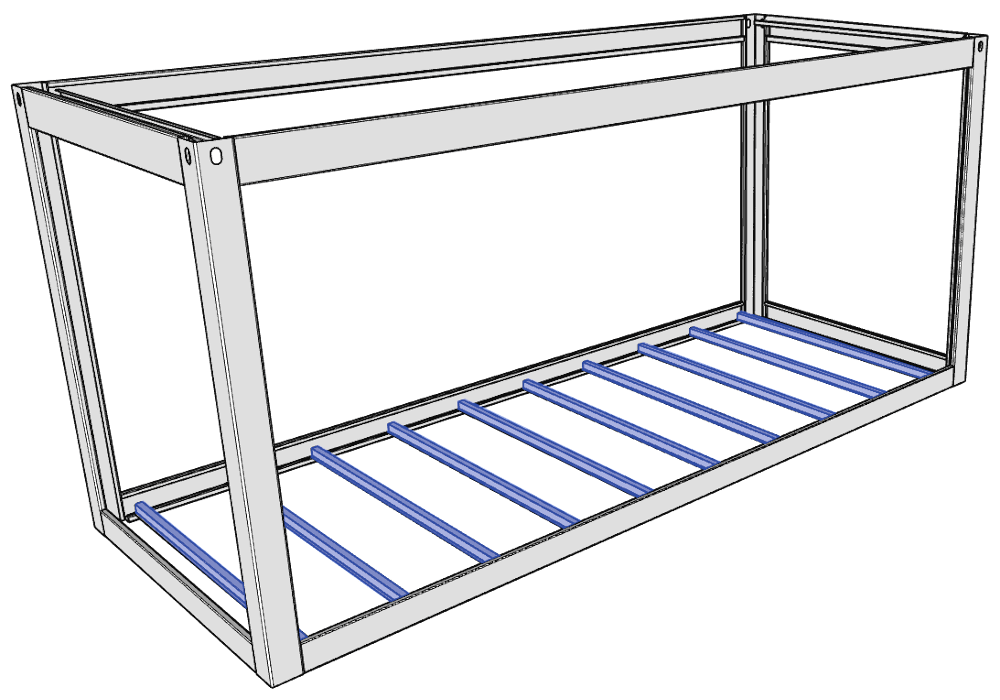
Transport holes
An important element of the container frame are also special oval transport holes with a rolled edge. The fold strengthens the edge of the hole and prevents tearing of the sheet when lifting the container. The holes are usually made at the ends of the uprights.
Hole dimensions 50 x 75mm.
The solution we propose is not only functional and practical, but also very aesthetic. In addition, it reduces the cost of building the container because there is no need to use additional elements, the so-called “container corners (cubes)” in the corners of the container
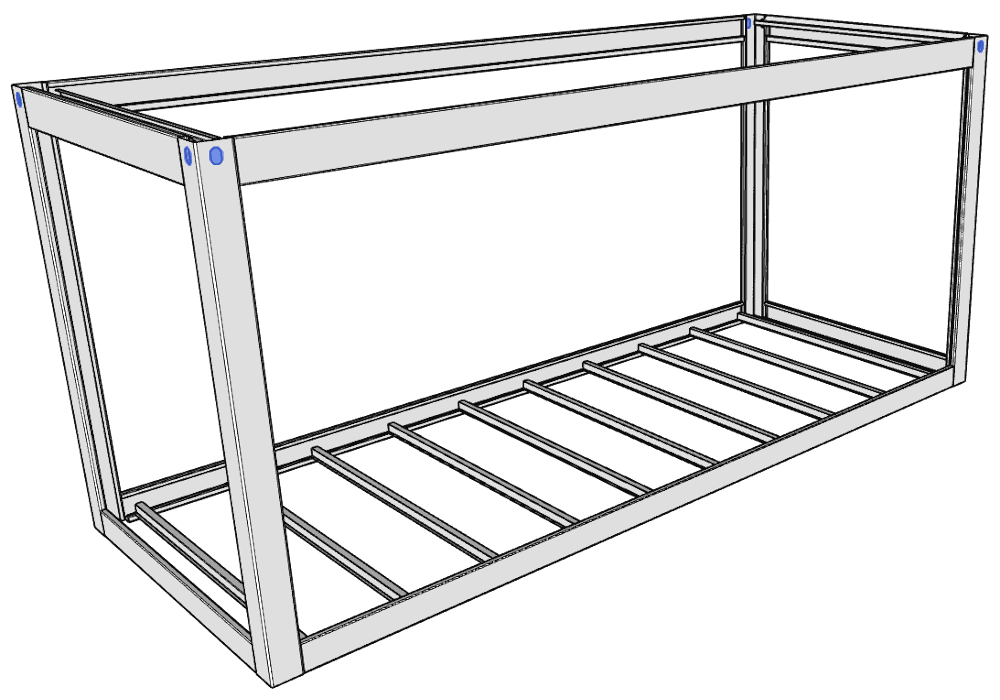
Roof sheathing
The culmination of the entire structure is the roof sheathing of the container. They can be made in different ways. Our proposal is based on cold-formed sections. We present two solutions:
- flat sheet metal sheathing with standing seam connection
- trapezoidal sheeting
Flat sheet sheathing is most often made of 1.0 mm thick galvanized sheet metal. It is a simple, effective and economical solution, moreover, the zinc coating is also a protection against corrosion.
The second type of sheathing with trapezoidal sheet is made of “black” steel sheet due to the subsequent welding of individual elements. The most commonly used sheet is 1.5 mm thick. After processing, the entire surface of the sheet metal is protected with protective paint coats.
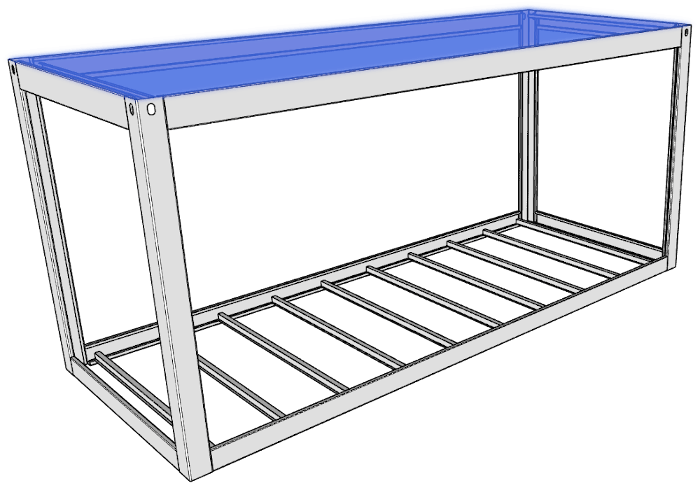
Façades
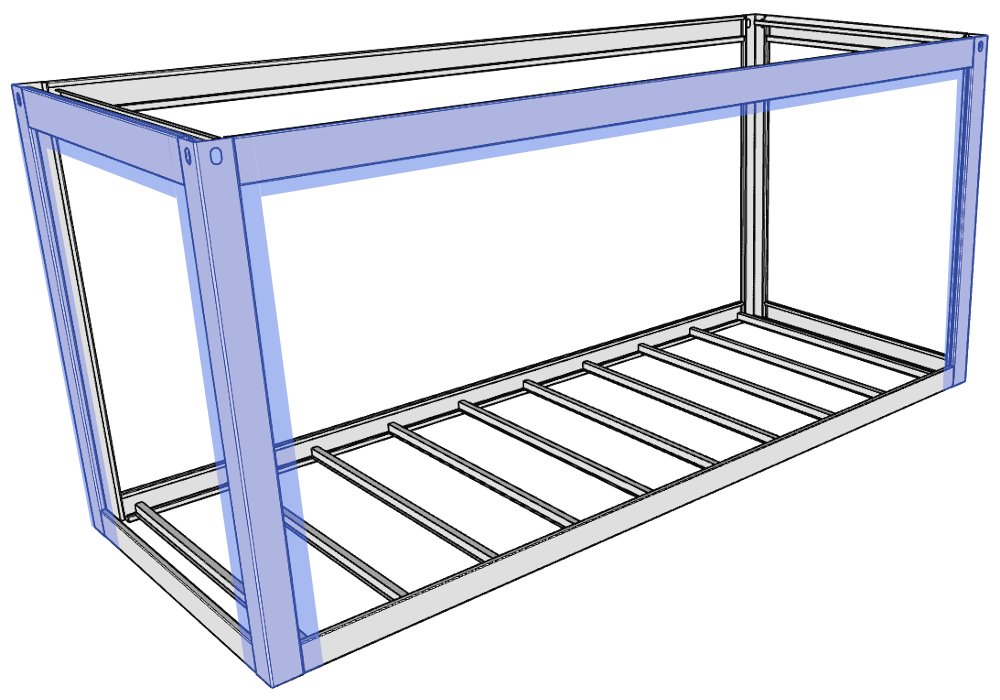
Schrag is not responsible for the correct selection of individual elements, both in terms of assembly and statics.
PROMOTIONAL VIDEO
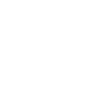